Custom Communications Cases & Containers
Advanced Packaging’s communication equipment cases and containers provide superior protection and convenient portability for all kinds of deployable communications systems. Certified packaging engineers design and manufacture precision customized foam inserts guaranteed to securely hold and protect your system. API partners with all the different industries that rely on deployable communication systems, including broadcasting, the department of defense, and rural medical communications, just to name a few.
Reusable, Compact Solutions
API designs and constructs custom reusable shipping cases and containers to allow for the fast set up and tear down of all types of communication components. Whether the need is for a large-scale network, flyaway SATCOM system, or a small production studio, API can work with you to configure the perfect solution. Tactical mobile radios used in first responder communication, chargers, antennae, RF monitoring, BGAN, or mobile satellite dish containers, we can create a custom solution to satisfy your specific needs.
A SYSTEM WITHIN A Custom Case
Advanced Packaging understands the importance associated with having a system that can functionally work within a case. That is why we have a dedicated department and staff, with extensive knowledge in the field of systems integration. Through the merger of our core competencies: protective case development, wire and cable harness assembly, precision metal fabrication, and conceptual design; API provides turn-key integration solutions for the fielding of both portable and fixed-site systems.
Brand Awareness / Product Launch
API appreciates the importance and impact that addition of custom graphics and logos to a case or container can do for brand awareness. Our professionals will work with you during the design and engineering process to determine the best method or format for your project.
With all of these services available under one roof, we can provide our customer base with a single resource, capable of fulfilling every aspect of their project’s needs. Advanced Packaging is “Not Just Cases, Total Solutions.” Experience matters put our 50-plus years of case and container design and manufacturing to work for you.
Examples of Our Custom Cases & Containers
Understanding The API Design Process

Phase 1: Collaboration
The first step in Advanced Packaging Inc.’s (API) engineering and design process is the collaboration phase. During this phase, clients meet with API’s team to transform their ideas into custom solutions. API’s commitment to quality is underscored by their AS9100 certification, and their vertical integration ensures they can provide a comprehensive range of services. Unlike typical packaging companies, API employs three full-time engineers dedicated to meeting all customer needs, showcasing their expertise and mature approach to engineering and manufacturing.
Phase 2: Research
The second step in API’s design and engineering process is the research phase. During this stage, the API team conducts an in-depth study of the client’s equipment, focusing on dimensions, applications, and transportation methods. This comprehensive research enables API to select the most suitable custom solution tailored to the client’s specific needs.
Phase 3: Development & Design Phase
The third step in API’s process is the development and design phase. Building on the insights gathered during the research phase, API’s engineers utilize advanced software to create detailed renderings of the custom case or container. These digital renderings visually represent the proposed solution, ensuring that every aspect of the design is tailored to the client’s specific equipment, dimensions, applications, and transportation needs.
Phase 4: Draw Concept
Once the development and design phase is approved by the client, the engineers at API move forward with creating a detailed, realistic concept of the custom solution. This concept drawing provides a more accurate and tangible representation of what the final case or container will look like, allowing the client to visualize the end product and ensure it meets their expectations before production begins.
Phase 5: Create a Proof
The fifth step in API’s process is the creation of a proof. At this stage, the API team transforms the research and design concepts into a physical proof. This proof serves as a preliminary version of the final product, allowing clients to evaluate and provide feedback on the design and functionality. The proof ensures that the solution meets all requirements and expectations before proceeding to full-scale production.
Phase 6: Manufacture
After the proof has been successfully completed, our manufacturing team begins producing the exact number of cases and containers required. Each case is meticulously designed and engineered to match the precise specifications outlined in the proof, ensuring consistency and quality in the final products.
Phase 7: Quality Control
Before the cases are delivered to the end user, each one undergoes a rigorous quality control phase. During this stage, an API team member carefully inspects each case to ensure it not only meets all specified requirements but also exceeds our stringent internal standards. This thorough inspection process guarantees that every case is built to perform reliably, time and time again.
Phase 8: Deliver
The final step in the process is the delivery phase. In this stage, API ensures that your custom solution is safely delivered to your location. We coordinate all logistics to ensure your cases or containers arrive on time and in perfect condition. This phase marks the successful completion of the project, with your custom-engineered solution ready to serve its purpose.
Testimonials
I just wanted to let you know that our instrument fit into the API case very nicely. Both will be on their way to Johnson Space Center in Houston tomorrow. Thanks for the fine effort and the timely delivery!
Randy Hammond
Johns Hopkins University
Our Partners
Meet Our Team
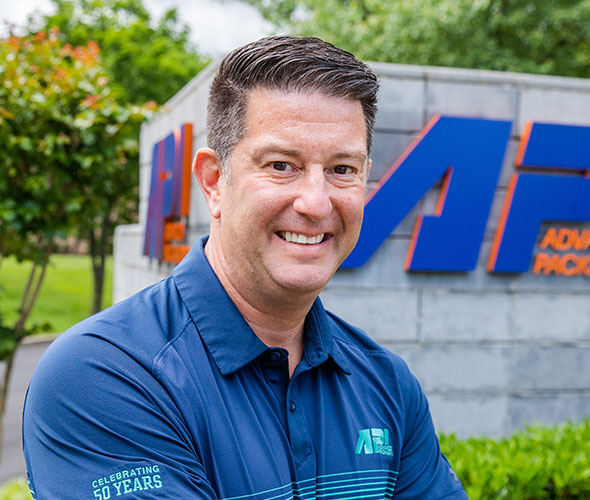
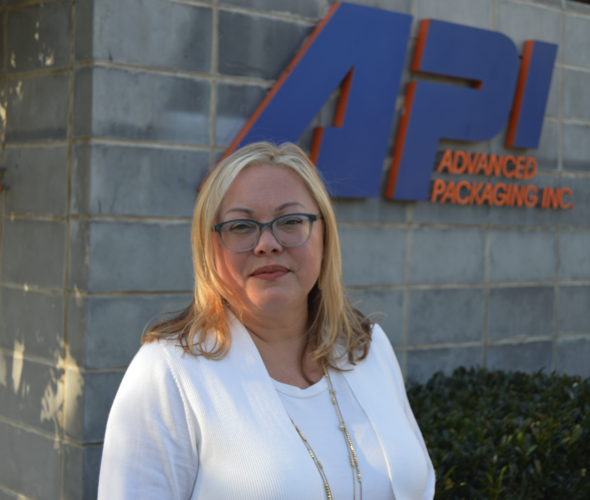
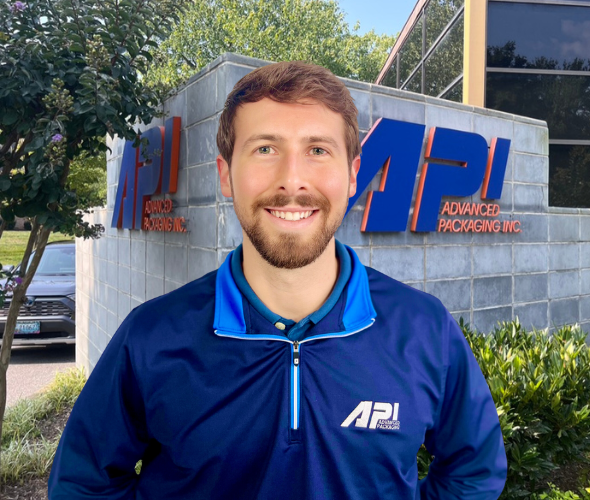